

The next step is to cut out the leaves. Twenty-six gauge copper sheet is pretty thin so I usually just use metal shears. But with this one I also used a jewelry saw because it has a tricky inside curve that can be hard to navigate cleanly with shears.
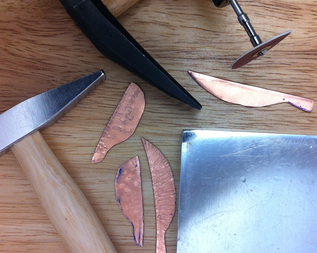
Also shown is a steel block on which I hammer the piece, a couple of typical fold-forming hammers, and the head of a rotary tool with a sanding disk to help smooth sharp cut edges. It's optional at this stage but you'll need to do some edge smoothing before you're finished. Sometimes I wait until the end to clean up a piece but it seems more often I do lots of little cleanups as I go.
Ironically, that's almost always my plan for how I'll work in the studio, too. Just clean as you go, Nancy. Use a tool or material, then put it away. How simple! But it never continues through a whole project. At some point I always stop and look around in stunned silence. How did all that stuff get out, and over there, and over there, and under that? Don't let anyone tell you otherwise, kids. Creating art is NOT always pretty ... or even hygienic I suspect.
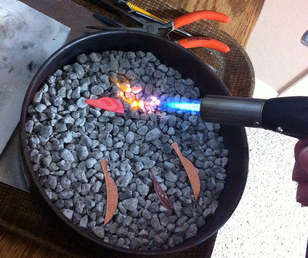
The final step for any of my earrings is always attaching argentium sterling silver earring wires. Argentium sterling is more expensive than regular sterling silver but the fact that it doesn't tarnish like traditional sterling makes it worth the extra cost. I switched to silver earwires for copper or bronze earrings, too, because many people seem to have skin problems with non-silver or gold earwires. I discovered that making them slim and quite simple helped insure the silver doesn't detract from the copper or bronze of the jewelry.
Clicking the pictures below will produce close ups of the earrings made for this blog post. Note how each are shaped uniquely and have different numbers and shapes of hammer blows. But the process to create them was essentially the same with only little tweaks at certain steps. I do love how copper moves! While you can fold form many metals (given strong enough tools and arms) copper has the ideal metal moving properties for this technique.
These earrings, along with a number of other new pieces, will be available in my AuSable Designs shop at the AuSable Artisan Village Gallery (AAV) this week.
I'll be teaching Fold Forming classes this fall through the AAV Gallery and Art Center. They'll include additional things not detailed in this post along with lots of tips and hands-on practice. The classes will be small (4-5 students max) and held in my Roscommon jewelry studio. You will sign up through the AAV and the fees help support the non-profit center. More information will be available both on this site and the AAV site in early fall of 2014.